Analysis of Mechanical Properties and Microstructure of Aluminum and Copper Sheet Welding Using Friction Stir Spot Welding Method
DOI:
https://doi.org/10.35814/asiimetrik.v6i1.5552Keywords:
FSSW, microstructure, mechanical, spot weldingAbstract
Welding aluminum and copper materials using friction stir spot welding (FSSW) is widely practiced. Although strong enough, it still produces keyhole and shoulder marks, which are quite large due to the large shoulder and pin sizes. This study investigates the joining of aluminum and copper panels using the FSSW technique using smaller shoulders and pins in different shoulder shapes. The study began by cutting aluminum and copper panels 150 mm long, 50 mm wide, and 5 mm thick. The joining process was carried out at rotational speeds of 900, 1200, and 1500 rpm with tools with several variations in pin length. Pin lengths of 0, 5, and 7 mm with pin diameters made the same at 5 mm, shoulder diameter 20 mm. The connection was observed for macrostructure, microstructure, and hardness. Different tool geometries have the potential to be applied in FSSW joints, especially for sheets. The highest hardness value is found in Cu-Cu material welding, with an average hardness value of 101.63 HVN in the stir zone area. The lowest hardness value is located in the base metal of aluminum material, with an average hardness value of 48.37 HVN.
Downloads
References
Akramifard, H.R. et al. (2014) ‘Microstructure and mechanical properties of Cu/SiC metal matrix composite fabricated via friction stir processing’, Materials & Design (1980-2015), 54, pp. 838–844.
Almaxco, A. (2015) Aluminium Alloy 1100 - H18, Almaxco. Available at: https://almaxco.com/wp-content/uploads/2023/06/Aluminium-Alloy-AA-1100.pdf (Accessed: 15 May 2023).
Andrade, D.G. et al. (2021) ‘Shoulder Related Temperature Thresholds in FSSW of Aluminium Alloys’, Materials, 14(16), p. 4375.
ASTM, A. (2017) ‘ASTM E384-17: Standard Test Method for Microindentation Hardness of Materials’. Available at: https://www.astm.org/e0384-17.html (Accessed: 9 January 2023).
Benyerou, D. et al. (2021) ‘Parametric Study Of Friction Stir Spot Welding (FSSW) For Polymer Materials Case Of High Density Polyethylene Sheets: Experimental And Numerical Study’, Frattura ed Integrità Strutturale, 15(55).
Bilici, M.K. (2012) ‘Effect of tool geometry on friction stir spot welding of polypropylene sheets’, eXPRESS Polymer Letters, 6(10), pp. 805–813.
Çam, G., Javaheri, V. and Heidarzadeh, A. (2023) ‘Advances in FSW and FSSW of dissimilar Al-alloy plates’, Journal of Adhesion Science and Technology, 37(2), pp. 162–194.
Esmaeili, A., Givi, M.K.B. and Rajani, H.R.Z. (2011) ‘A metallurgical and mechanical study on dissimilar Friction Stir welding of aluminum 1050 to brass (CuZn30)’, Materials Science and Engineering: A, 528(22), pp. 7093–7102.
Feizollahi, V. and Moghadam, A.H. (2023) ‘Effect of pin geometry, rotational speed, and dwell time of tool in dissimilar joints of low-carbon galvanized steel and aluminum 6061-T6 by friction stir spot welding’, Results in Materials, 20, p. 100483.
Lewise, K.A.S. and Dhas, J.E.R. (2022) ‘FSSW process parameter optimization for AA2024 and AA7075 alloy’, Materials and Manufacturing Processes, 37(1), pp. 34–42.
Li, W. et al. (2014) ‘Improving mechanical properties of pinless friction stir spot welded joints by eliminating hook defect’, Materials & Design (1980-2015), 62, pp. 247–254.
Meschut, G., Janzen, V. and Olfermann, T. (2014) ‘Innovative and Highly Productive Joining Technologies for Multi-Material Lightweight Car Body Structures’, Journal of Materials Engineering and Performance, 23(5), pp. 1515–1523.
Nugroho, A.W., Saputra, M.R.D. and Budiyantoro, C. (2019) ‘Pengaruh Kecepatan Putar Tool dan Sudut Shoulder Sambungan Friction Stir Spot Welding pada Bahan Polypropylene’, Semesta Teknika, 22(2), pp. 183–193.
Saputra, L.A., Sukarno, N.A. and Zulaehah, S. (2021) ‘Pengaruh Interlayer Elektroplating Zinc pada Kekuatan Mekanik Friction Stir Spot Welding Aa1100-Ss400’, Semesta Teknika, 24(2), pp. 93–101.
Sehono and Ardianto, H. (2021) ‘Efek Friction Stir Spot Welding Dalam Pemasangan Rivet Terhadap Sifat Mekanik Material Almunium Seri 2024’, Teknika STTKD: Jurnal Teknik, Elektronik, Engine, 7(2), pp. 184–192.
Shen, Z. et al. (2021) ‘Refill Friction Stir Spot Welding Al Alloy to Copper via Pure Metallurgical Joining Mechanism’, Chinese Journal of Mechanical Engineering, 34(1), p. 75.
Shen, Z., Ding, Y. and Gerlich, A.P. (2020) ‘Advances in friction stir spot welding’, Critical Reviews in Solid State and Materials Sciences, 45(6), pp. 457–534.
Tiwan, Ilman, M.N., and Kusmono (2021) ‘Microstructure and mechanical properties of friction stir spot welded AA5052-H112 aluminum alloy’, Heliyon, 7(2), p. e06009.
Venukumar, S. et al. (2014) ‘Microstructural and Mechanical Properties of Walking Friction Stir Spot Welded AA 6061-T6 Sheets’, Procedia Materials Science, 6, pp. 656–665.
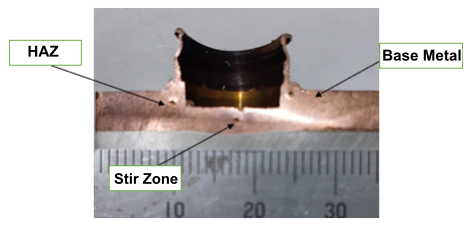