Experimental and Numerical Testing of Jaw Gripper Design Using The Mass Reduction Method of Onyx-Carbon Fiber Material at PT. Matahari Megah
DOI:
https://doi.org/10.35814/asiimetrik.v6i2.6147Keywords:
jaw gripper, optimal, testing system, deflectionAbstract
A robot arm is a robot component in the motion subsystem of a robot system to determine the position and orient the object so that the robot can perform certain tasks, such as picking and placing an object. To use it as a pick and place, a gripper shaped like a human finger, commonly called a jaw gripper, is required, which is used to hold, tighten, hold, and release an object. The shape of the jaw gripper is designed and made according to the shape of the workpiece to be grasped, which was created by PT Matahari Megah using the 3D-printing method for its customer. The jaw gripper that has been designed still needs to be developed to produce a more optimal jaw gripper design, such as by reducing the use of excessive filament without reducing quality and minimizing costs incurred. Therefore, a more optimized jaw gripper test tool was made with a material reduction method using the generative design process in Inventor software, and physical testing was carried out on the ability to grip and deflection, compared to the testing process using a test system that had been designed with a dial gauge measuring instrument. The results of the comparison between the Inventor software results and the simulation results do not exceed 10%, with the difference at a pressure of 2 bars of 7% and the difference at a pressure of 4.6/5 bars of 1.87%.
Downloads
References
Basori, Syafrizal and Suharwanto (2015) ‘Analisis Defleksi Batang Lentur Menggunakan Tumpuan Jepit dan Rolpada Material Aluminium 6063 Profil U dengan Beban Terdistribusi’, Jurnal Konversi Energi dan Manufaktur, 2(1), pp. 50–58.
Hassan, M. and Baqar, M. (2015) ‘Design and Implementation of a DTMF Based Pick and Place Robotic Arm’, Asian Journal of Engineering, Sciences & Technology, 5(1), pp. 8–12.
Hendito, M., Halim, A. and Siahan, E. (2023) ‘Physical Characterization of Onyx-Carbon Fiber Reinforced Material using Taguchi Method’, International Journal of Innovative Science and Research Technology (IJISRT), 8(6), pp. 3322–3326.
Jabbar, A.A. and Yasdar, Y. (2022) ‘Sistem Kendali Gripper Adaptif Pada Robot Transporter’, Jurnal Mosfet, 2(2), pp. 26–31.
Markforged (2024) About Eiger, About Eiger. Available at: https://support.markforged.com/portal/s/article/Eiger-Deployments (Accessed: 7 May 2024).
Maskatim and Baidlowi, M. (2022) ‘Kendali Pneumatic Pada Gripper Robot’, Jurnal Elektrosista, 10(1), pp. 61–74.
Pedersen, M.R. et al. (2016) ‘Robot skills for manufacturing: From concept to industrial deployment’, Robotics and Computer-Integrated Manufacturing, 37, pp. 282–291.
Rahmawan, A., Munadi, M. and Prahasto, T. (2013) ‘Optimasi Gripper Dua Lengan dengan Menggunakan Metode Genetic Algorithm pada Simulator Arm Robot 5 DOF (Degree of Freedom)’, Jurnal Teknik Mesin, 1(2), pp. 9–16.
Raynaldo, K. et al. (2020) ‘Automation Systems In Automatic Assembling Gear Shaft Output As Car Gearbox Part At PT. Matahari Megah’, in IOP Conference Series: Materials Science and Engineering. 3rd Tarumanagara International Conference of the Applications of Technology and Engineering (TICATE), Jakarta, Indonesia: Universitas Tarumanagara, p. 012050.
Romano, J.M. et al. (2011) ‘Human-Inspired Robotic Grasp Control With Tactile Sensing’, IEEE Transactions on Robotics, 27(6), pp. 1067–1079.
Satria, D. and Wati, L. (2019) ‘Prototype Robot Lengan Pemindah Barang Dengan Kendali Lengan Manusia Berbasis Arduino Uno’, Jurnal Ilmu Komputer dan Bisnis, 10(1), pp. 2126–2134.
Schunk (2023a) PGN 50-1, Gripping System. Available at: https://schunk.com/in/en/gripping-systems/parallel-gripper/pgn/pgn-50-1/p/000000000000370099 (Accessed: 5 January 2024).
Schunk (2023b) PGN 64-1, Gripping System. Available at: https://schunk.com/in/en/gripping-systems/parallel-gripper/pgn/pgn-64-1/p/000000000000370100 (Accessed: 4 January 2024).
Singh, P., Kumar, A. and Vashisth, M. (2013) ‘Design of a Robotic Arm with Gripper & End Effector for Spot Welding’, Universal Journal of Mechanical Engineering, 1(3), pp. 92–97.
Suhandar, G.A., Halim, A. and Raynaldo, K. (2023) ‘Optimasi Dan Analisis Desain Jaw Gripper Menggunakan Filamen Onyx Di PT. Matahari Megah’, Jurnal Serina Sains, Teknik dan Kedokteran, 1(1), pp. 133–140.
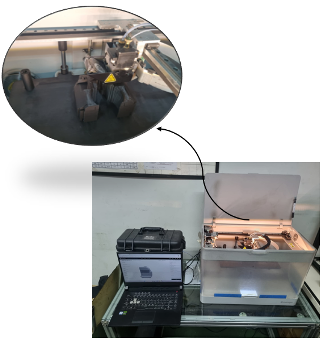