Flow Investigation Inside the Vacuum Gripper for Labeling Application with Dimensions of 100 mm × 100 mm Using the CFD Method
DOI:
https://doi.org/10.35814/asiimetrik.v6i2.6160Keywords:
automation, vacuum gripper, labelAbstract
Nowadays, the application of automation in the manufacturing sector is important to increase production efficiency. One of the variations in industrial automation is the vacuum gripper. Vacuum grippers are specifically designed to handle specific workpieces, such as labeling application. Label characteristics that easily bend and stick to the workpiece when peeled off require a specific gripper. This research was carried out using 2 methods, experimental method and CFD simulation method. The experimental method was carried out by collecting pressure data with Arduino. Data from this experiment will be used for the CFD simulation. Based on these experimental tests, the average vacuum pressure obtained was -44.372 kPa. From the simulation vacuum pressure on the 12 inlet holes was obtained. The largest vacuum pressure was at inlet 12 with a vacuum pressure value of -44372.11 Pa, while the smallest was at inlet hole 1 with a value of -44371.86 Pa. The pressure distribution is evenly distributed at all the suction point and has suited the design requirements.
Downloads
References
Alipour, N., Shahgholi, G. and Jahanbakhshi, A. (2022) ‘Evaluation and comparison and the performance of pressurized and vacuum cylindrical distributors in soybean cultivation’, Results in Engineering, 16, p. 100546.
Bahamon, J. and Martinez, M. (2023) ‘Study of Fluid-Dynamic Behavior In A Convergent–Divergent Nozzle by Shape Optimization using Evolutionary Strategies Algorithms’, in Proceedings of the Institution of Mechanical Engineers, Part G: Journal of Aerospace Engineering. The Institution of Mechanical Engineers, Los Angeles, USA: The Institution of Mechanical Engineers (12), pp. 2844–2862.
Darmawan, S. and Tanujaya, H. (2019) ‘CFD Investigation of Flow Over a Backward-facing Step using an RNG k-? Turbulence Model’, International Journal of Technology, 10(2), pp. 280–289.
Gabriel, F., Bobka, P. and Dröder, K. (2020) ‘Model-Based Design of Energy-Efficient Vacuum-Based Handling Processes’, Procedia CIRP, 93, pp. 538–543..
Hirose, S. and Umetani, Y. (1978) ‘The Development Of Soft Gripper For The Versatile Robot Hand’, Mechanism and Machine Theory, 13(3), pp. 351–359.
Jaiswal, A.K. and Kumar, B. (2017) ‘Vacuum Gripper-an Important Material Handling Tool’, International Journal of Science & Technology, 7(1), pp. 1–8.
Lee, S.H. et al. (2022) ‘Passive air leakage detection mechanism for enhanced vacuum suction actuator efficiency’, Microsystem Technologies, 28(10), pp. 2353–2359.
Leschziner, M.A. (2020) ‘Friction-Drag Reduction by Transverse Wall Motion – A Review’, Journal of Mechanics, 36(5), pp. 649–663.
Lintermann, A. (2021) ‘Computational Meshing for CFD Simulations’, in K. Inthavong et al. (eds) Clinical and Biomedical Engineering in the Human Nose: A Computational Fluid Dynamics Approach. Singapore: Springer, pp. 85–115.
Michael, V., Halim, A. and Irawan, A.P. (2020) ‘Design of pick and place and color sorting system using VDI 2221’, in IOP Conference Series: Materials Science and Engineering. 3rd Tarumanagara International Conference of the Applications of Technology and Engineering (TICATE) 2020, Jakarta, Indonesia: Universitas Tarumanagara, p. 012165.
Papadakis, E. et al. (2020) ‘On the Use of Vacuum Technology for Applied Robotic Systems’, in 6th International Conference on Mechatronics and Robotics Engineering (ICMRE). 2020 6th International Conference on Mechatronics and Robotics Engineering (ICMRE), pp. 73–77.
Pham, D.T. and Yeo, S.H. (1988) ‘A knowledge-based system for robot gripper selection: criteria for choosing grippers and surfaces for gripping’, International Journal of Machine Tools and Manufacture, 28(4), pp. 301–313.
Phuyal, S., Bista, D. and Bista, R. (2020) ‘Challenges, Opportunities and Future Directions of Smart Manufacturing: A State of Art Review’, Sustainable Futures, 2, p. 100023.
Sanei, S.H., Arndt, A. and Doles, R. (2020) ‘Open Hole Tensile Testing of 3D Printed Continuous Carbon Fiber Reinforced Composites’, Journal of Composite Materials, 54(20), pp. 2687–2695.
Stegmaier, V. et al. (2023) ‘A Behavior Model for Digital Twins of Vacuum Suction Cups’, Procedia CIRP, 118, pp. 958–963.
Suprapto and Widodo, S. (2017) Pengenalan Teknologi Vakum. 1st edn. Yogyakarta, Indonesia: Pustaka Pelajar. [Print].
Urbano, D.G. et al. (2021) ‘A Semi-Empirical Fluid Dynamic Model of a Vacuum Microgripper Based on CFD Analysis’, Applied Sciences, 11(16), p. 7482.
Wang, Z., Makiyama, Y. and Hirai, S. (2021) ‘A Soft Needle Gripper Capable of Grasping and Piercing for Handling Food Materials’, Journal of Robotics and Mechatronics, 33(4), pp. 935–943.
Yaqub, K. et al. (2021) ‘Design, Simulation and Implementation of An Efficient Vacuum System and Gas Load Calculations for A 6 Mev Industrial LINAC’, Vacuum, 187, p. 110151.
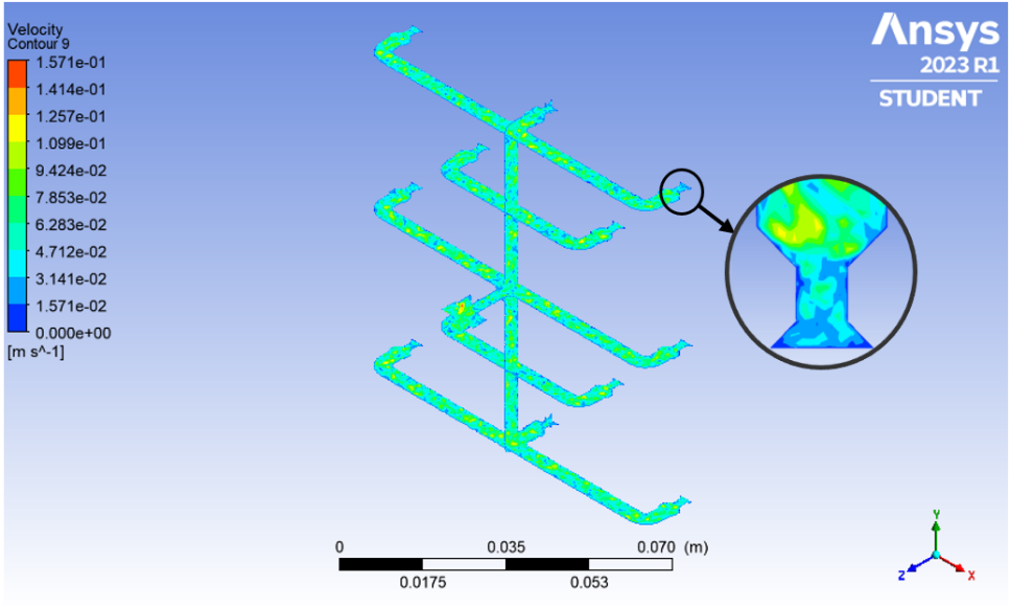