Utilization of Single and Double Orifice Plates in Pipe Inner Flow Structure by Computational Method
DOI:
https://doi.org/10.35814/asiimetrik.v7i1.7913Keywords:
orifice, flow structure, Reynolds number, recirculation, vortexAbstract
The orifice plate is a device that disrupts the flow in the pipe. The disturbed flow results in the formation of flow structures. The flow structure formed can be utilized for several applications such as multi-fluid mixing and microbubble generator. Using orifice plates to utilize the flow structure results in more significant pressure loss. This study aims to identify the characteristics of the flow structure generated by single and double orifice plates with 1D and 2D spacing at various Reynolds numbers, namely Re = 1×104, 5×104, 1×105, and 5×105, as a basis for application in these various applications. The results show that single and double orifice plates can produce flow structure phenomena such as recirculation and vortex regions. The recirculation area is formed smaller in the double orifice plate due to the flow that is separated faster to converge back to the pipe wall but broader so that the flow of the orifice plate is narrower. Increasing the applied Reynold's number causes the separated flow to reconnect to the pipe wall faster, resulting in a smaller recirculation area. Double orifice plates are more suitable for applications that require a certain degree of mixing or pressure distribution, but with a consequent more significant pressure loss. Meanwhile, single plates can be used for simple needs with little pressure loss.
Downloads
References
Abed, N. et al. (2020) ‘Experimental And Numerical Investigations For Turbulent Air Flow Characteristics Of Circular Orifice Plate’, IOP Conference Series: Materials Science and Engineering, 881(1), p. 012050. Available at: https://doi.org/10.1088/1757-899X/881/1/012050.
Ahmed, S. et al. (2023) ‘Design Modification In An Industrial Multistage Orifice To Avoid Cavitation Using CFD Simulation’, Journal of the Taiwan Institute of Chemical Engineers, 148, p. 104833. Available at: https://doi.org/10.1016/j.jtice.2023.104833.
Araoye, A.A., Badr, H.M. and Ahmed, W.H. (2017) ‘Investigation Of Flow Through Multi-Stage Restricting Orifices’, Annals of Nuclear Energy, 104, pp. 75–90. Available at: https://doi.org/10.1016/j.anucene.2017.02.002.
Bikić, S. et al. (2022) ‘Comparison Of Single-Hole And Multi-Hole Orifice Energy Consumption’, Advances in Mechanical Engineering, 14(1), pp. 1–13. Available at: https://doi.org/10.1177/16878140221075461.
Collins, A. and Clark, S. (2022) ‘Additional Data Supporting The 2022 Updates To The ISO 5167 Standards’, Flow Measurement and Instrumentation, 86, p. 102193. Available at: https://doi.org/10.1016/j.flowmeasinst.2022.102193.
Đurđević, M. et al. (2019) ‘Experimental Research Of Single-Hole And Multi-Hole Orifice Gas Flow Meters’, Flow Measurement and Instrumentation, 70, p. 101650. Available at: https://doi.org/10.1016/j.flowmeasinst.2019.101650.
Düz, H. (2021) ‘Effect Of Conical Angle On The Hydraulic Properties Of Orifice Plate Flows: A Numerical Approach’, Flow Measurement and Instrumentation, 81, p. 102026. Available at: https://doi.org/10.1016/j.flowmeasinst.2021.102026.
Iskandar, W. et al. (2022) ‘Study of Airfoil Characteristics on NACA 4415 with Reynolds Number Variations’, International Review on Modelling and Simulations (IREMOS), 15(3), pp. 162–171. Available at: https://doi.org/10.15866/iremos.v15i3.21684.
Julian, J., Iskandar, W., Wahyuni, F. and Ferdyanto, F. (2022) ‘Computational Fluid Dynamics Analysis Based On The Fluid Flow Separation Point On The Upper Side Of The NACA 0015 Air-foil With The Coefficient of Friction’, Media Mesin: Majalah Teknik Mesin, 23(2), pp. 70–82. Available at: https://doi.org/10.23917/mesin.v23i2.18217.
Julian, J., Iskandar, W., Wahyuni, F., Armansyah, A., et al. (2022) ‘Effect of Single Slat and Double Slat on Aerodynamic Performance of NACA 4415’, International Journal of Marine Engineering Innovation and Research, 7(2), pp. 93–100. Available at: https://doi.org/10.12962/j25481479.v7i2.12875.
Julian, J. et al. (2023) ‘The Effect of Micro Geometry with Various Forms as Passive Flow Control in NACA 4415’, Jurnal Asiimetrik: Jurnal Ilmiah Rekayasa & Inovasi, 5(2), pp. 231–242. Available at: https://doi.org/10.35814/asiimetrik.v5i2.4678.
Julian, J. et al. (2024) ‘Numerical Analysis of Gurney Flap Impact on NACA 4415 Airfoil Aerodynamics Performance’, Jurnal Asiimetrik: Jurnal Ilmiah Rekayasa & Inovasi, 6(1), pp. 121–132. Available at: https://doi.org/10.35814/asiimetrik.v6i1.5722.
Julian, J., Anggara, R.A. and Wahyuni, F. (2023) ‘Influence of Slat Size Variation as Passive Flow Control Instruments on NACA 4415 Airfoil Toward Aerodynamic Performance’, International Journal of Marine Engineering Innovation and Research, 8(2), pp. 367–375. Available at: https://doi.org/10.12962/j25481479.v8i2.16427.
Julian, J., Anggara, R.A. and Wahyuni, F. (2024) ‘Numerical Study On Characteristics Of The Backward-Facing Step Flow With Variations Of The Slope Angle Of The Step’, Jurnal Polimesin, 22(1), pp. 6–14. Available at: https://doi.org/10.30811/jpl.v22i1.4052.
Julian, J., Iskandar, W. and Wahyuni, F. (2022) ‘Aerodynamics Improvement of NACA 0015 by Using Co-Flow Jet’, International Journal of Marine Engineering Innovation and Research, 7(4), pp. 284–291. Available at: https://doi.org/10.12962/j25481479.v7i4.14898.
Julian, J., Iskandar, W. and Wahyuni, F. (2023) ‘Leading Edge Modification of NACA 0015 and NACA 4415 Inspired by Beluga Whale’, International Journal of Marine Engineering Innovation and Research, 8(2), pp. 222–231. Available at: https://doi.org/10.12962/j25481479.v8i2.16432.
Juwana, W.E. et al. (2019) ‘Hydrodynamic Characteristics Of The Microbubble Dissolution In Liquid Using Orifice Type Microbubble Generator’, Chemical Engineering Research and Design, 141, pp. 436–448. Available at: https://doi.org/10.1016/j.cherd.2018.11.017.
Lukiano, M.F. et al. (2023) ‘The Influence of Mounting Angle on Gurney Flap on The Aerodynamics Performance of NACA 0015 Using CFD Method’, International Journal of Marine Engineering Innovation and Research, 8(4), pp. 694–702. Available at: https://doi.org/10.12962/j25481479.v8i4.18891.
Nasiruddin, S. and Singh, S.N. (2021) ‘Performance Evaluation Of An Innovative Design Modification Of An Orifice Meter’, Flow Measurement and Instrumentation, 80, p. 101944. Available at: https://doi.org/10.1016/j.flowmeasinst.2021.101944.
Shaaban, S. (2014) ‘Optimization Of Orifice Meter’s Energy Consumption’, Chemical Engineering Research and Design, 92(6), pp. 1005–1015. Available at: https://doi.org/10.1016/j.cherd.2013.08.022.
Shah, M.S. et al. (2012) ‘Analysis Of Flow Through An Orifice Meter: CFD Simulation’, Chemical Engineering Science, 71, pp. 300–309. Available at: https://doi.org/10.1016/j.ces.2011.11.022.
Shan, F. et al. (2016) ‘Effects Of The Orifice To Pipe Diameter Ratio On Orifice Flows’, Chemical Engineering Science, 152, pp. 497–506. Available at: https://doi.org/10.1016/j.ces.2016.06.050.
Vemulapalli, S. and Venkata, S.K. (2022) ‘Parametric Analysis Of Orifice Plates On Measurement Of Flow: A Review’, Ain Shams Engineering Journal, 13(3), p. 101639. Available at: https://doi.org/10.1016/j.asej.2021.11.008.
Xie, W.A. and Xi, G.N. (2017) ‘Fluid Flow And Heat Transfer Characteristics Of Separation And Reattachment Flow Over A Backward-Facing Step’, International Journal of Refrigeration, 74, pp. 177–189. Available at: https://doi.org/10.1016/j.ijrefrig.2016.10.006.
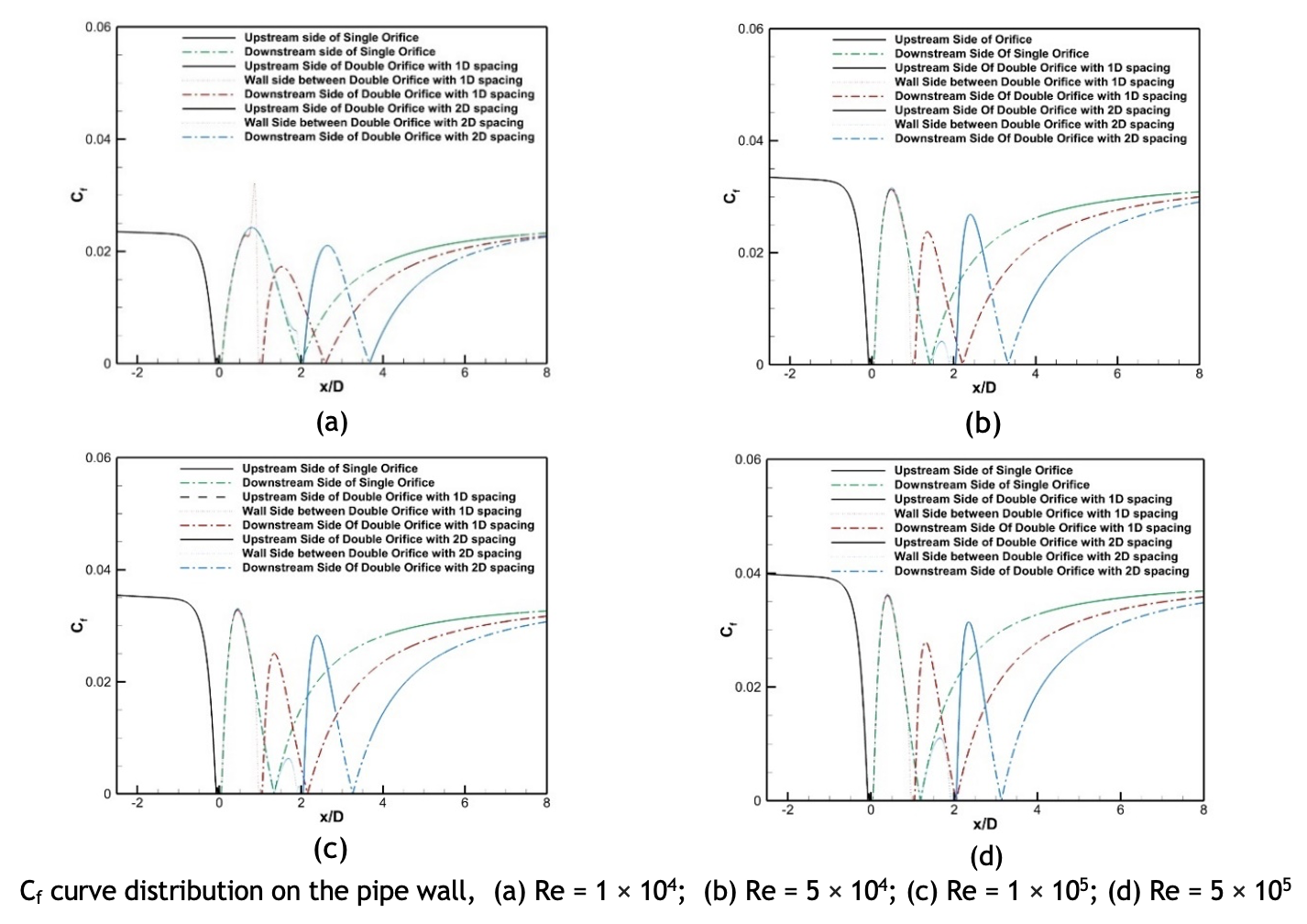